
Trendy Layered Short Hair 2019 Thick and graduation layers, if you want a voluminous look, this hair style fits you exactly. The ProX DMP 320 direct metal 3D printer is optimized for producing complex, chemically-pure titanium, stainless steel, or nickel super alloy parts.Just a new short haircut Or a new color too Let’s take a look at the recommendations of this year’s most underrated short hairstyles 1. Guests are treated to salon experiences that leave them feeling confident in their fashionable new looks, all thanks to our highly trained, professional stylists.F21 Canada Coupon Code, lowes 20 off coupon may 2019, how to use manufacturer coupons on peapod, zero coupon rate vs yield to maturity. Signature Style Salon brands are a collection of regional and national full-service hair salons that offer quality womens and mens haircuts, hair styling, and hair color services at an affordable price.
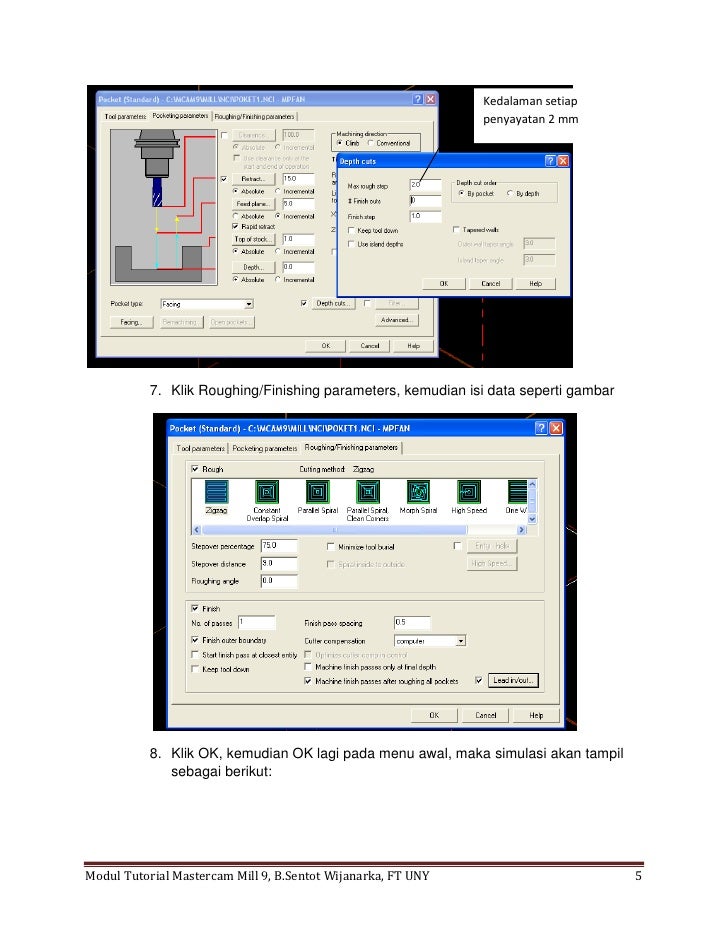
Intelligence gathered from the cut part and the machining process is applied for higher accuracy and efficiency. For extended tool life and cutting edge durability, all HPCMs have Helical’s APlus coating, designed for use in ferrous materials (up to 55Rc) and titanium.Vericut 8.0 enhancements increase the ability of manufacturing engineers to analyze, optimize, and document CNC programming and machining. Helical stocks HPCMs in 60°, 90°, and 120° angles, and 3- or 5-helical flutes. Engineered for increased running parameters, the chamfer mill saves time, increases metal removal rates, and improves longevity. 25ppm O2 during builds for high chemical purityHelical’s line of high performance chamfer mills (HPCMs) introduces a helically fluted design for free cutting and enhanced part finish.
Air Cut optimization built-in (off-part milling cutter motions) Organizes menus, options where previously found It operates independently, but can also be integrated with CAM systems.
Self-guided training sessions launch from welcome screen, automatically open associated sample files Method compares stock cutting position to 2D. Translate models via selecting solid model features Logger displays messages, reports in tabbed logger window Tool Manager preferences dialog allows default settings to streamline creation of cutting tool assemblies
Layout options can be selected for the task Create, save workflow for different jobs Enhanced modeling options for control, flexibility when moving individual models, assemblies, and component origins
A key target for those process improvements are time-consuming roughing activities.“It’s all in the roughing. Looks to improve productivity and competitiveness, it focuses on areas that won’t touch its quality and safety records. So when Connecticut-based supplier E.A. Integrates with online tool management systemsComponents that convey fuel, air, and hydraulic fluid in aerospace vehicles, equipment, and other applications are safety critical, so top quality manufacturing is a must.
Mastercam 2019 Aircut Software From CNC
The programming tools provide high metal removal rates, minimize cycle times, maximize tool life, and exploit the full capabilities of machine tools. Patten machinists apply Dynamic Motion CNC strategies of Mastercam CAD/CAM software from CNC Software Inc., Tolland, Connecticut. Patten Senior CNC Programmer Roger Dimmock.To improve roughing efficiency, E.A.
Final part diameter was about 1.6", and roughing operations removed about 3/4" per side. Part: T-shaped fitting with a central coupling connection, rough machined from 3" diameter Inconel 625 forging. Dynamic Motion technology is applicable to milling operations including facing, contouring, pocketing, and 3D roughing, as well as rough turning. Unconventional toolpaths reduce lateral forces and heat that accelerate tool and machine wear and can damage workpieces. Cutters move in arcs and circles, and avoid tight corners and deep tool engagements that magnify tool pressures.
Patten Senior CNC Programmer Roger Dimmock comments, “It cut the cycle time in half and the tool lasted 3x longer. Total roughing cycle time with Dynamic Motion: 17 min.E.A. The shallow radial depths of cut and simpler fixturing made it easier for the tool to reach some of the part’s tight features. With Dynamic Motion programming: Reduced tool pressures enabled application of a 3/4" diameter carbide endmill at an axial depth of cut of 1-1/2", with less-complex, less-restrictive fixturing. Total cycle time: 34 minutes. Initial tooling: Cobalt cutters for roughing at traditional speeds, feeds, and radial and axial depths of cut.
However, use of the technology has reduced cycle times 30% to 50% in most applications.“Depending on what type of tools we use, I’ve even seen times reduced 70% in some applications,” Dimmock says.Despite learning how to apply atypical parameters for Dynamic Motion machining, Dimmock says, “Working with the reseller and Mastercam, tech support was easy. Lower cutting forces enable high metal removal rates, even when machining delicate, thin-walled parts holding the parts in weaker fixtures using less powerful machine tools or operating tools at long extensions.Dimmock says he was skeptical when software reseller Macdac Engineering Inc.’s Alan Duprey recommended unfamiliar Dynamic Motion techniques. The increased cutting parameters improve productivity, and the lighter cuts decrease tool wear. Radial chip thinningThe software’s algorithms allow radial chip thinning, which calls for higher cutting speeds and feeds when cutter engagement falls below 50% of tool diameter – maintaining a constant chip load and optimal cutting temperatures.
You can’t just plow through them,” Dimmock says.He relies on tool supplier recommendations to determine the optimum amount of engagement for a particular tool in a particular material. The high-temp alloys and titanium are harder to cut. “In Inconel, I can take 5%, in stainless I can go up to 15% or 20%. The machinability of the workpiece material generally determines the appropriate stepover or percentage of the tool diameter that should be engaged in the workpiece. Once stock boundaries are entered, Mastercam figures everything else out.”Dimmock describes Dynamic Motion as an evolution of peel milling techniques in which the tool takes a small radial depth of cut, and a large axial depth of cut, at faster feed rates and higher spindle speeds and nibbles away at the part.“It is important to consider how much you can take off in one cut,” Dimmock says. The software has to know the stock boundaries and avoid regions, and the rest takes care of itself.
Initial tooling: conventional cobalt cutters. The thin flange prohibited use of aggressive machining parameters because heat and tool pressures would affect the flange’s flatness. Part: 316 stainless steel fitting, 2.6" x 2.4", with two flange ends, one thin, with 32Ra surface finish and ☐.003" flatness requirement.

